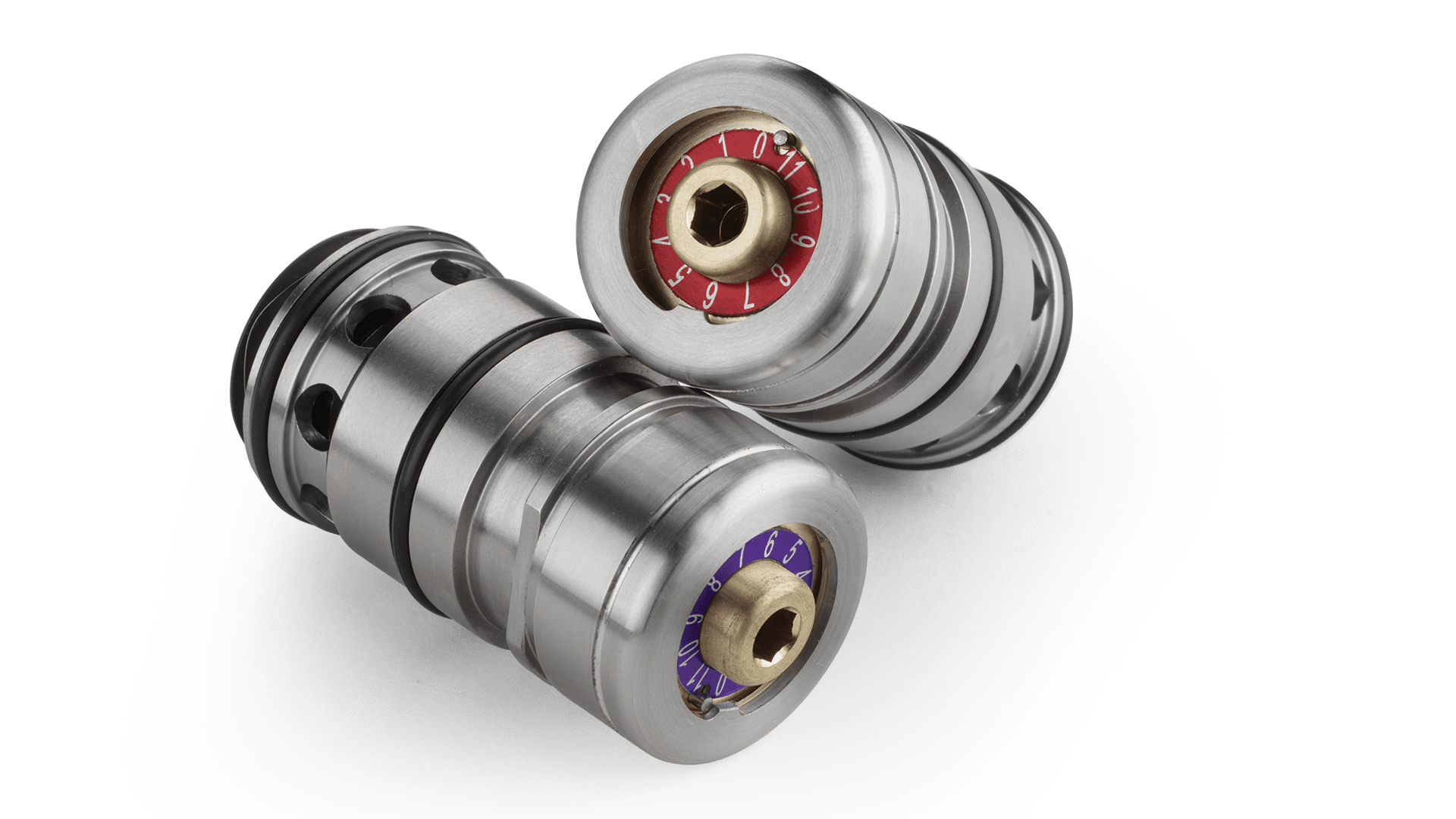
Multimatic DSSV™
In the Beginning…
What’s in a Name?
In 1996 Multimatic set the stage for a revolution in advanced vehicle dynamics development with its acquisition of a small but focused UK firm known as Dynamic Suspensions.
Founded in 1990, Dynamic Suspensions specialized in the design and development of dampers, advanced hydraulic systems, and the provision of engineering services to the European motorsports industry.
In 1997, Multimatic moved Dynamic Suspensions to a new Thetford, UK facility, later to be known as Multimatic Technical Centre Europe (MTCE). Bolstered with Multimatic’s engineering might and world-class resources, this would ultimately become the birthplace of DSSV. But in the meantime…
Dynamic Suspensions Shim Dampers
Since the 1950s, common automotive dampers have functioned via stacks of flexible shims. Performance characteristics of these dampers are impacted by a host of factors including: shim thickness, material properties and dimensional tolerances; variability in the assembly process, friction between shims in a stack, shim preload; locational tolerance of the orifices relative to the shims, dimensional tolerance of passage cross-sections, operating temperatures, and cleanliness of the assemblies.
From a damper tuning perspective, the combined effects of these many factors are difficult to accurately predict, especially after being compounded in use by shim fatigue and the buildup of wear-particulate trapped between shims.
In practical terms, accurate shim damper tuning is a time-consuming process, as an ideal shim configuration can only be found by rebuilding dampers with reconfigured shim stacks in a repetitive, trial-and-error process.
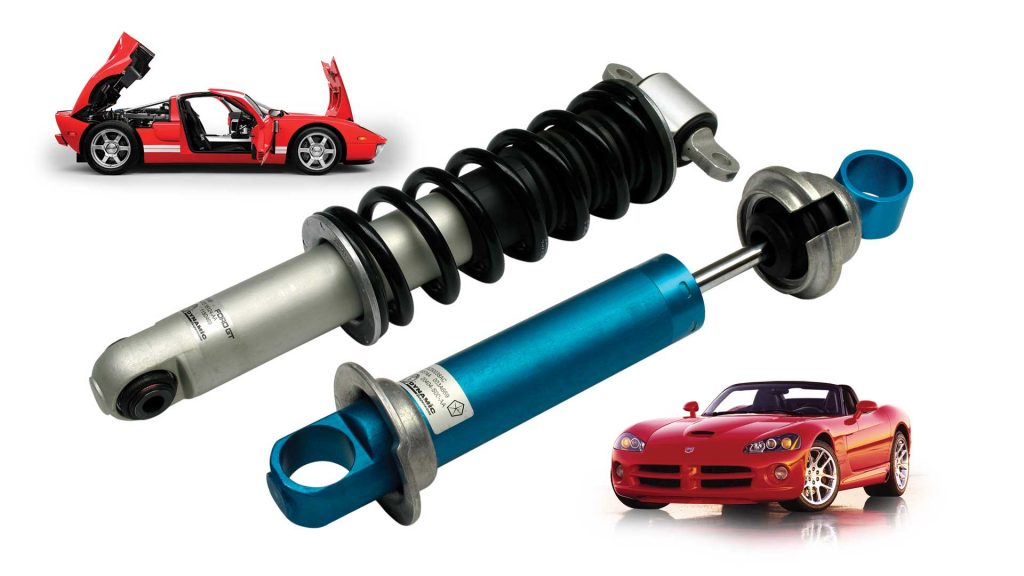
Multimatic Dynamic Suspensions supplied B1640 shim dampers to Ford for the GT (left), and to Chrysler for the third-generation Viper.
Even so, as refined by the experts at Multimatic Dynamic Suspensions, the shim damper carved out a successful competition niche. Launched in 2000, Dynamic Suspensions’ modular 1640 shim damper series achieved championship success in professional race series internationally.
Still, it was time to move on…
Damping Beyond the Shim
Conceived to address the noted shortcomings of shim dampers, the Dynamic Suspensions Spool Valve (DSSV) damper was inspired by directional control valves employed in modern hydraulic systems.
In lieu of shim stacks, Multimatic’s patented DSSV design determines damper Force/Velocity (F/V) characteristics by means of precisely machined circumferential ports in spool valves.
Putting this concept into practice faced an immediate hurdle: Considering the Lilliputian scale of the parts involved, it was practically impossible to achieve a properly shaped port using common machine tools. Larry Holt, Multimatic’s Chief Technical Officer, describes the challenge: “Think of a tiny little cylinder with a carefully shaped hole in its side which is opened by damper pressure against a tiny little spring with unbelievably challenging tolerances. A lot of companies would have given up after the first tolerance calculation, but we persevered.”
Translating this spool-valve damper concept into reality became feasible only after medical-grade Electrical Discharge Machining (EDM) capability was installed at Multimatic Technical Centre Europe (MTCE) in Thetford.
In testing, it soon became apparent that removing flexible shims from the equation not only allowed more predictable and consistent operation for each individual damper, but also minimized damper-to-damper variance. Consistent performance was realized across the range of suspension frequencies, even with highly digressive damping curves. This resulted from the spool valve mechanism’s relatively low inertia and reduced stiction, thanks in part to the relatively low gas pressures required. While traditional dampers rely on relatively high reservoir pressure to prevent oil cavitation below a threshold velocity, DSSV dampers are essentially ‘cavitation-proof’ by design, permitting lower reservoir pressures and improvements in ride comfort.
These low gas pressures also minimized ride height change resulting from temperature variation, while turbulent fluid-flow characteristics within the spool valve mechanism also minimized heat-induced damper fade: typical force degradation from 30°C to 120°C was found to be within 4% for DSSV dampers over a typical range of velocities, compared with up to 14% for poppet-valve dampers, and up to 16% for a conventional shim damper.
Damper re-valving was made quicker and easier with external, cartridge-based spool configurations. By eliminating the need to uninstall, disassemble, and rebuild the damper, remote-cartridge DSSV dampers effectively moved the re-valving process from paddock to pit lane. Having two spool valves per damper also fully decoupled the compression and rebound force-velocity curves. The days of the ‘shim shuffler’ were numbered.
Mathematical Prediction
Prominent among the DSSV design’s advantages is that its damping characteristics are accurately predictable using the math of governing hydraulic equations. This prompted the parallel development of Multimatic’s proprietary SpecFinder™ software, offering a suite of capabilities that includes quickly matching spool valve configurations to a customer’s desired damping characteristics. In theory, then, this DSSV hardware/software system would deliver unparalleled Force/Velocity predictability, plus on-car tunability that would be a race engineer’s dream. But only actual motorsport would provide the true litmus test for Multimatic’s spool valve concept.
SpecFinder™
Imagine software that enables DSSV customers to quickly and accurately select spool valve configurations tailored to their project’s desired damping characteristics. That’s SpecFinder. Then picture a program that permits graphic visualization of the range of on-car bump and rebound adjustments available through that current spool selection. That’s also SpecFinder – basically a fully predictive damper model, doubling as a software damper dyno.
By eliminating the trial-and-error guesswork of flexible shim stacks, SpecFinder and DSSV lessen dependence on trackside damper dynamometers, and drastically reduce the time between an idea and a ready damper.