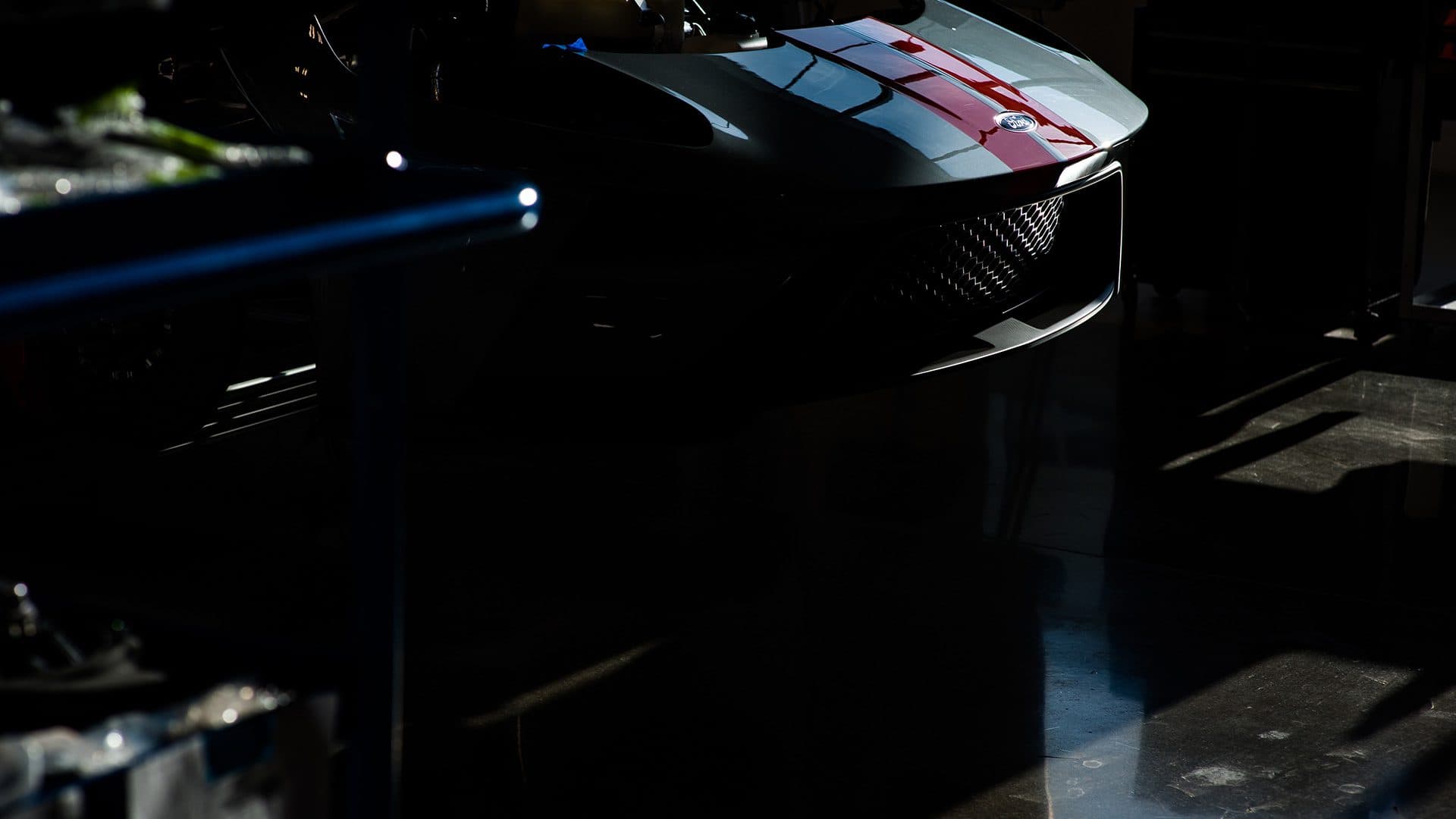
Proven and Validated
MISA is our approach to solving the biggest challenges.
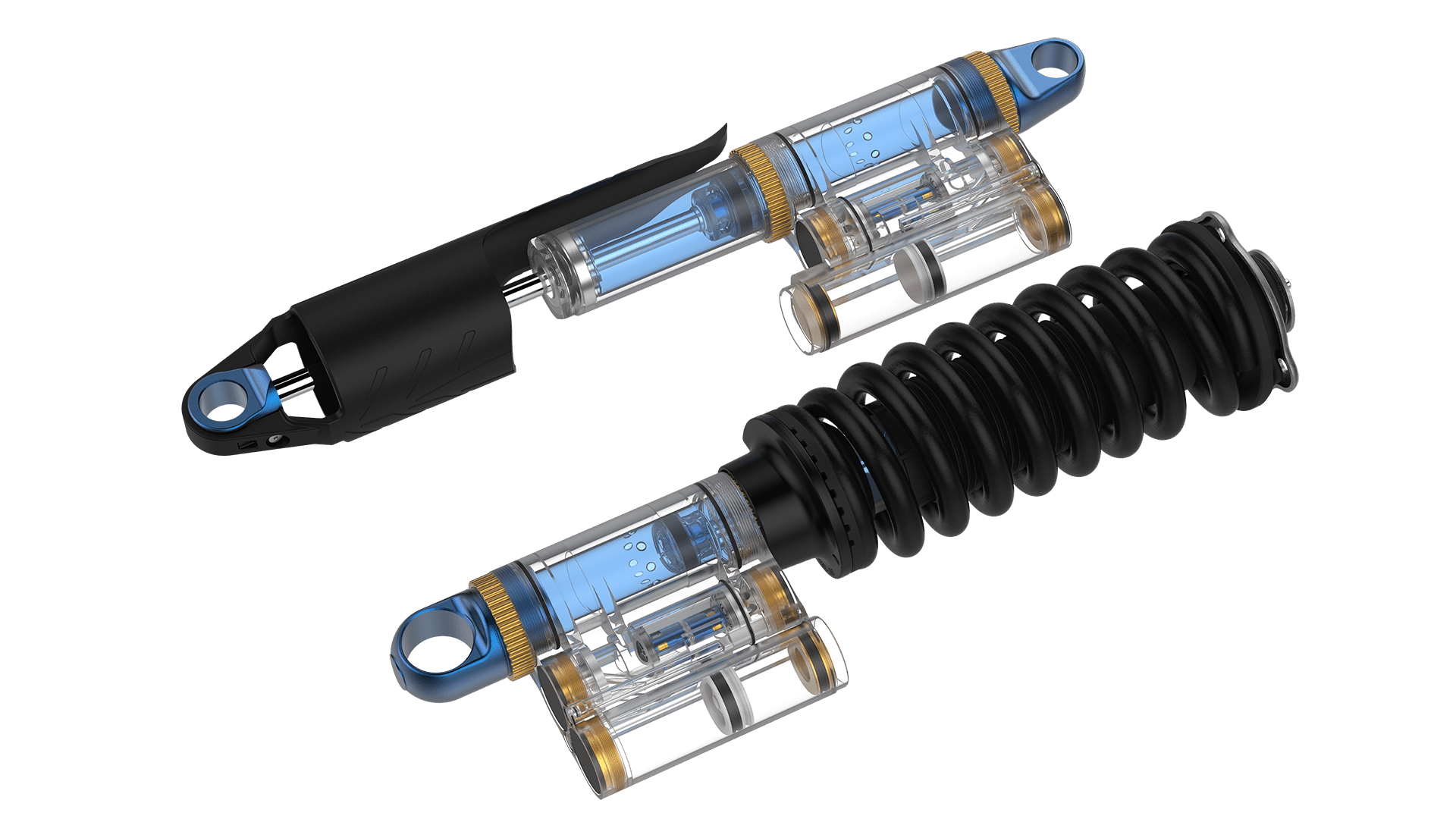
Achieving the nearly impossible.
Synthesis. Validation. Correlation.
MISA changes “trial & error” to “define & optimize”.
This sequence illustrates MISA’s value in the development of Multimatic DSSV™ dampers for the Chevrolet Colorado ZR2 pickup.
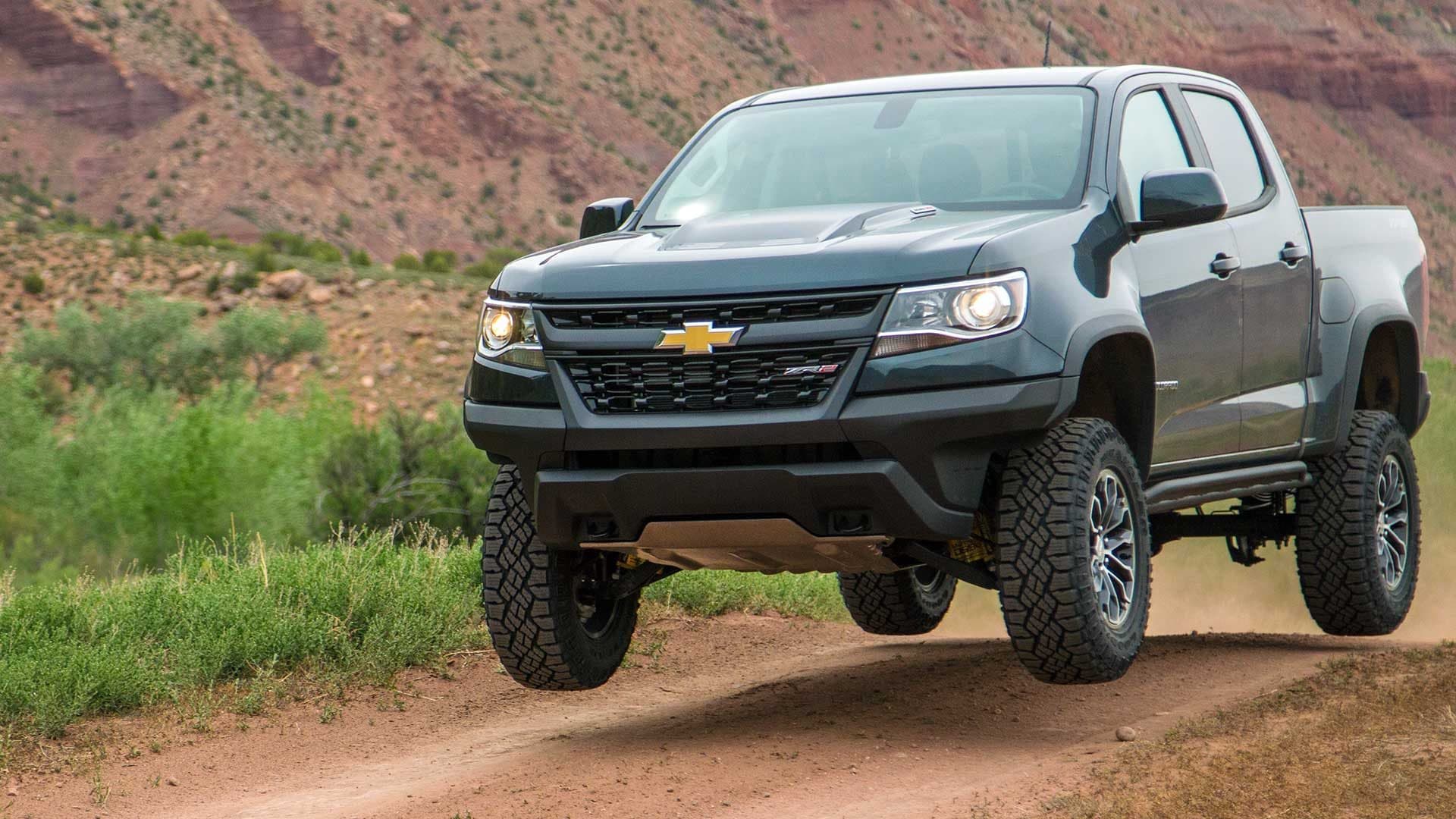
5. Validation: Vehicle-Level Testing
Dampers were installed on ZR2 prototypes and tested in real-world conditions including on-road driving, rock crawling and high-speed desert running. Performance was then compared against the original complete-vehicle specifications.
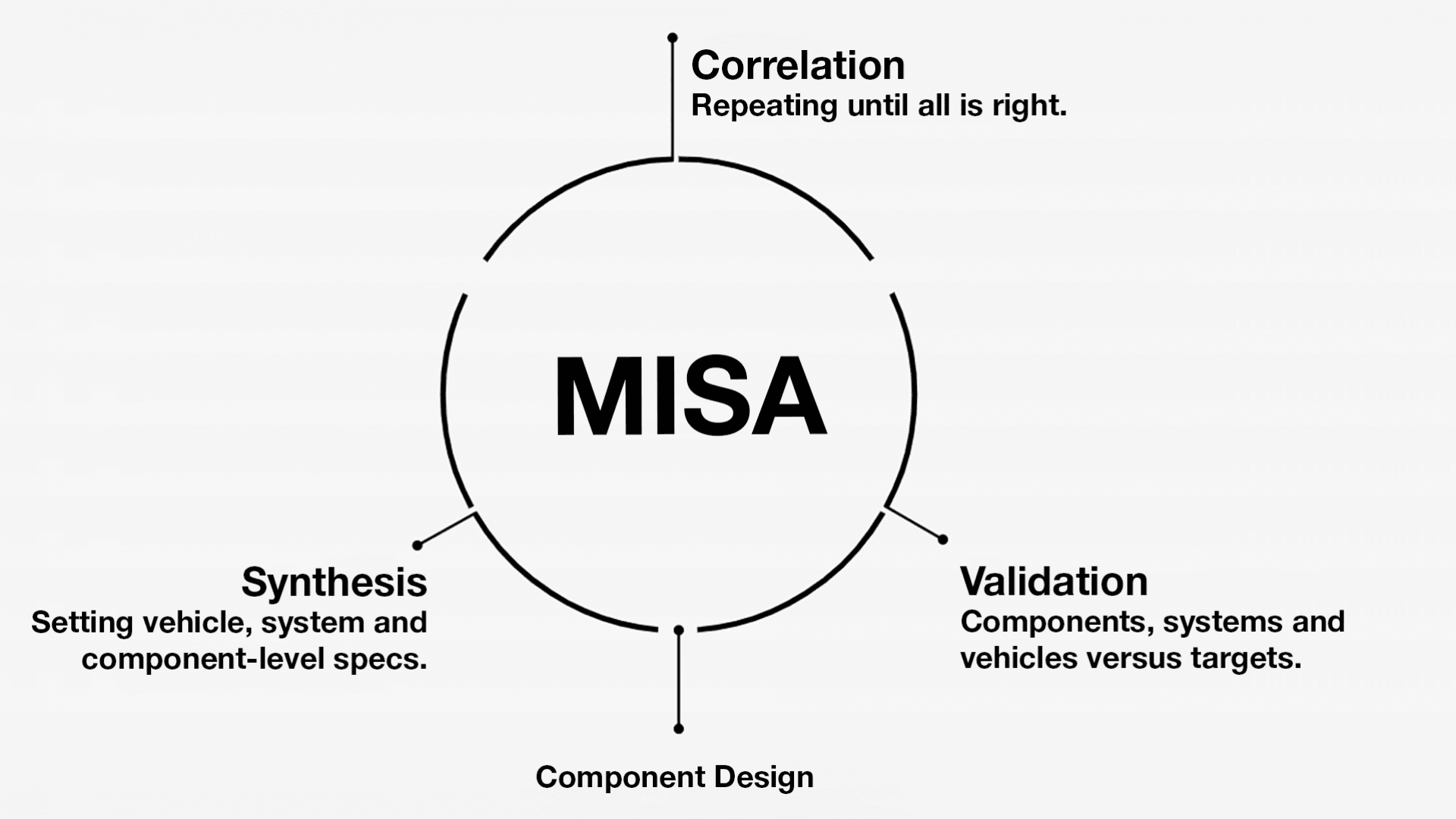
6. Correlation: Testing vs. Design Brief / Specification
Product and vehicle development is a repetitive process. MISA clearly defines targets and expectations, and then verifies achievements. The process identifies issues at all levels, to enable rapid problem solving.
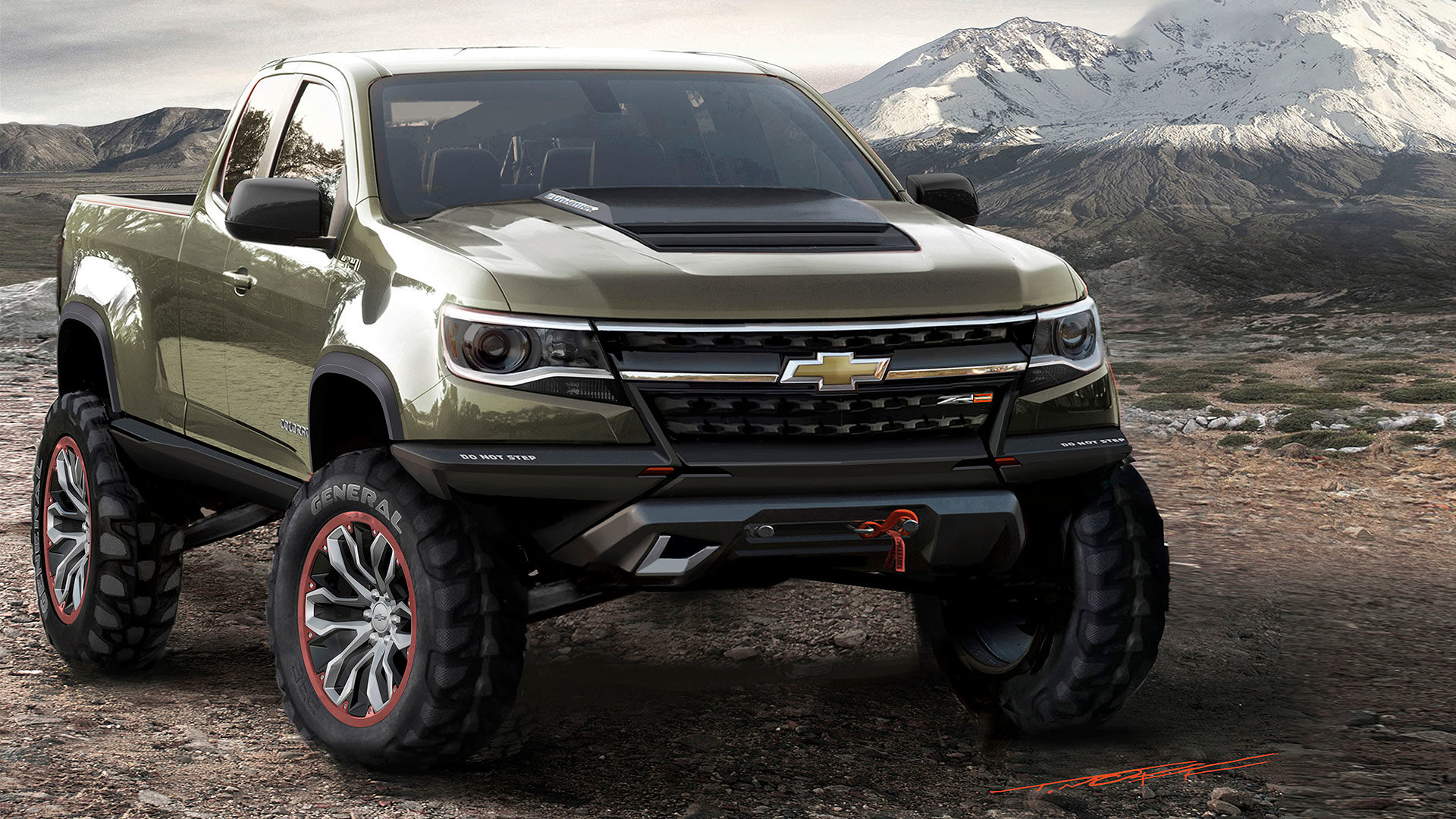
1. Synthesis: Design Brief and Vehicle-Level Specification
In collaboration with GM, the initial “Synthesis” phase defined a design brief and vehicle-level specification. This became the target against which vehicle performance was later measured.
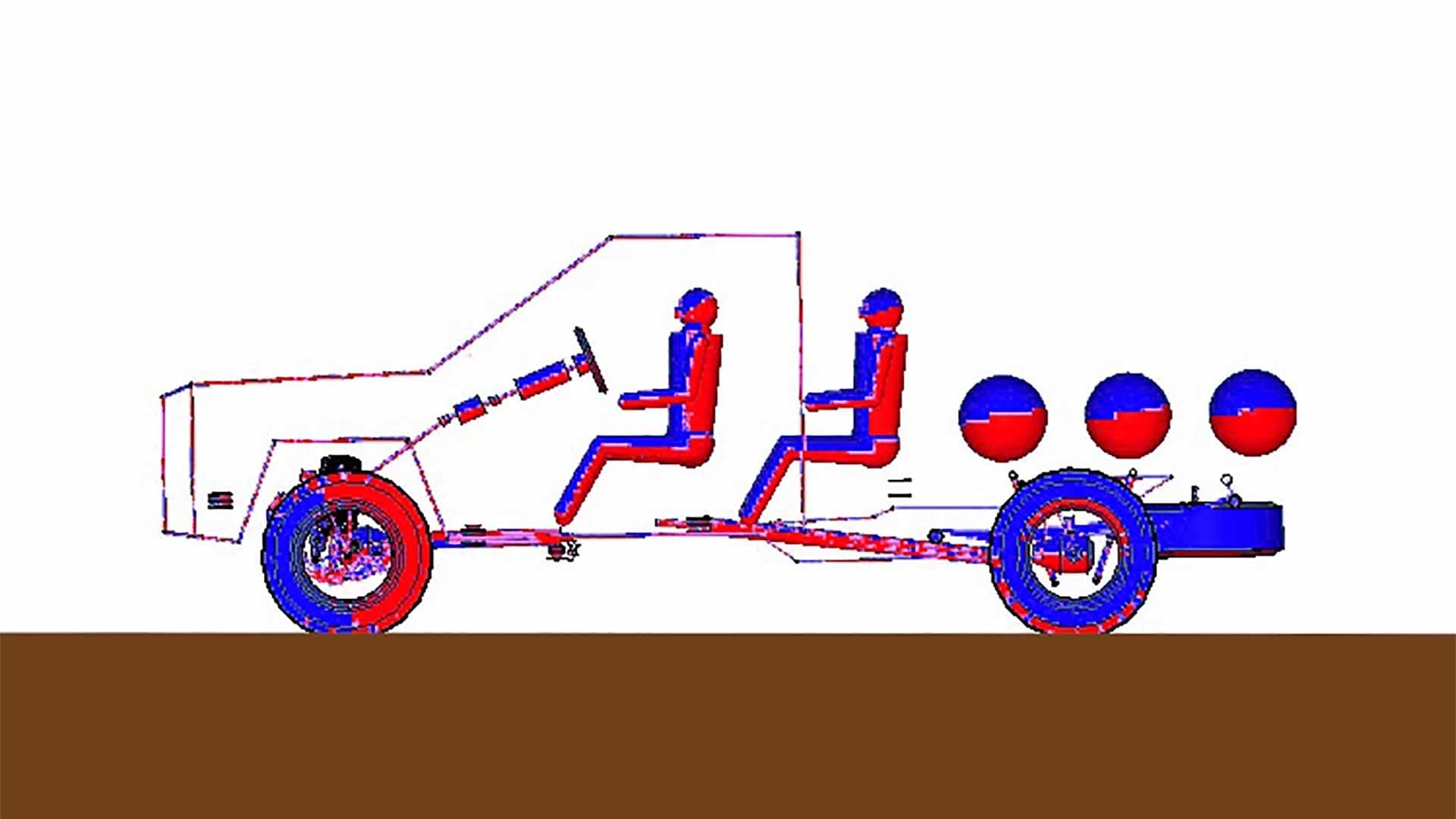
2. Synthesis: System- and Component-Level Specifications
In part two of the Synthesis phase, we analyzed all affected vehicle systems to develop system- and component-level specifications. System- and component-level performance were later measured against these targets.
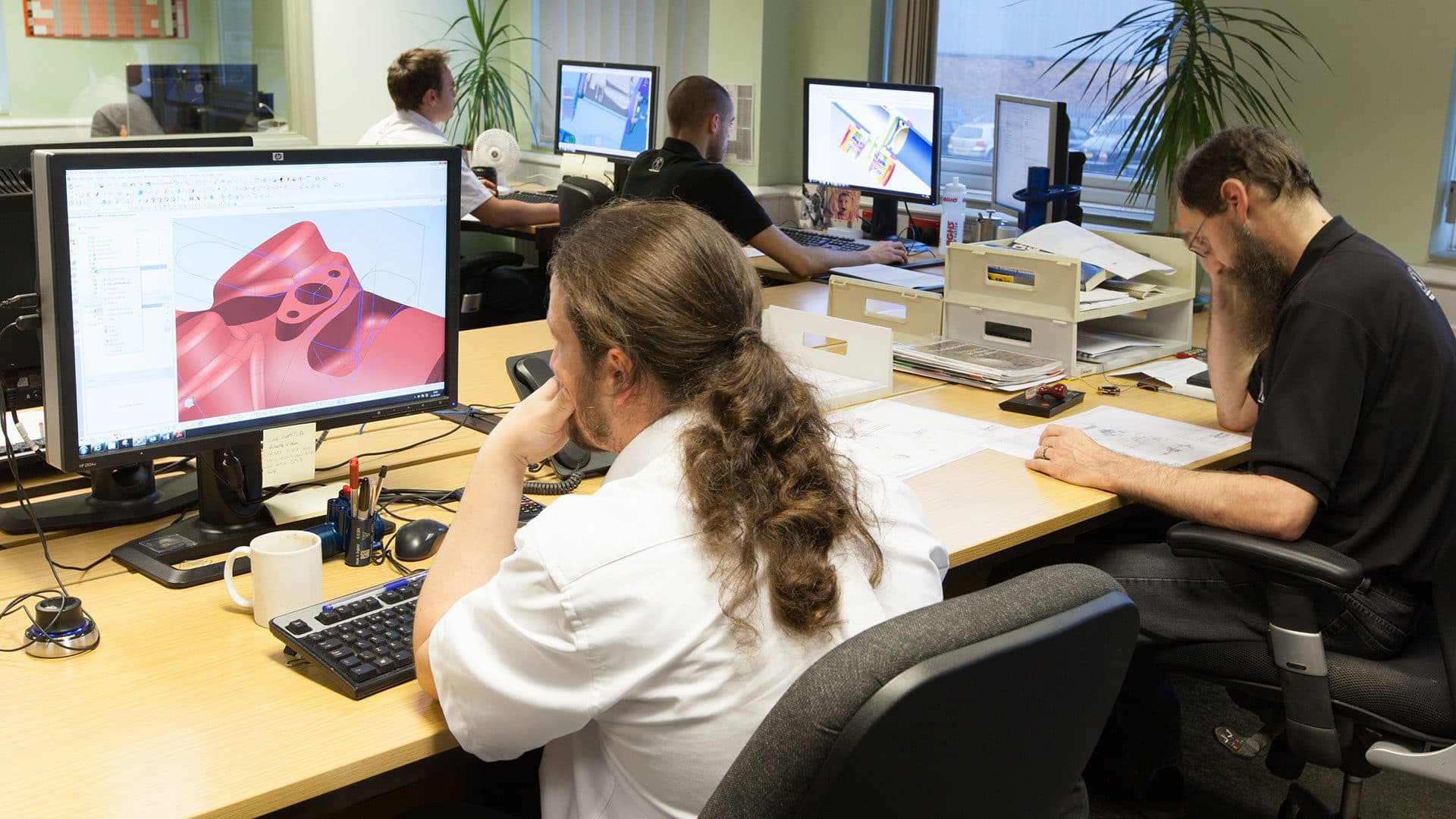
3. Component Design and Engineering
With specifications established, we moved into the design and engineering phase to develop a new Multimatic DSSV damper aimed at meeting the component-level specification.
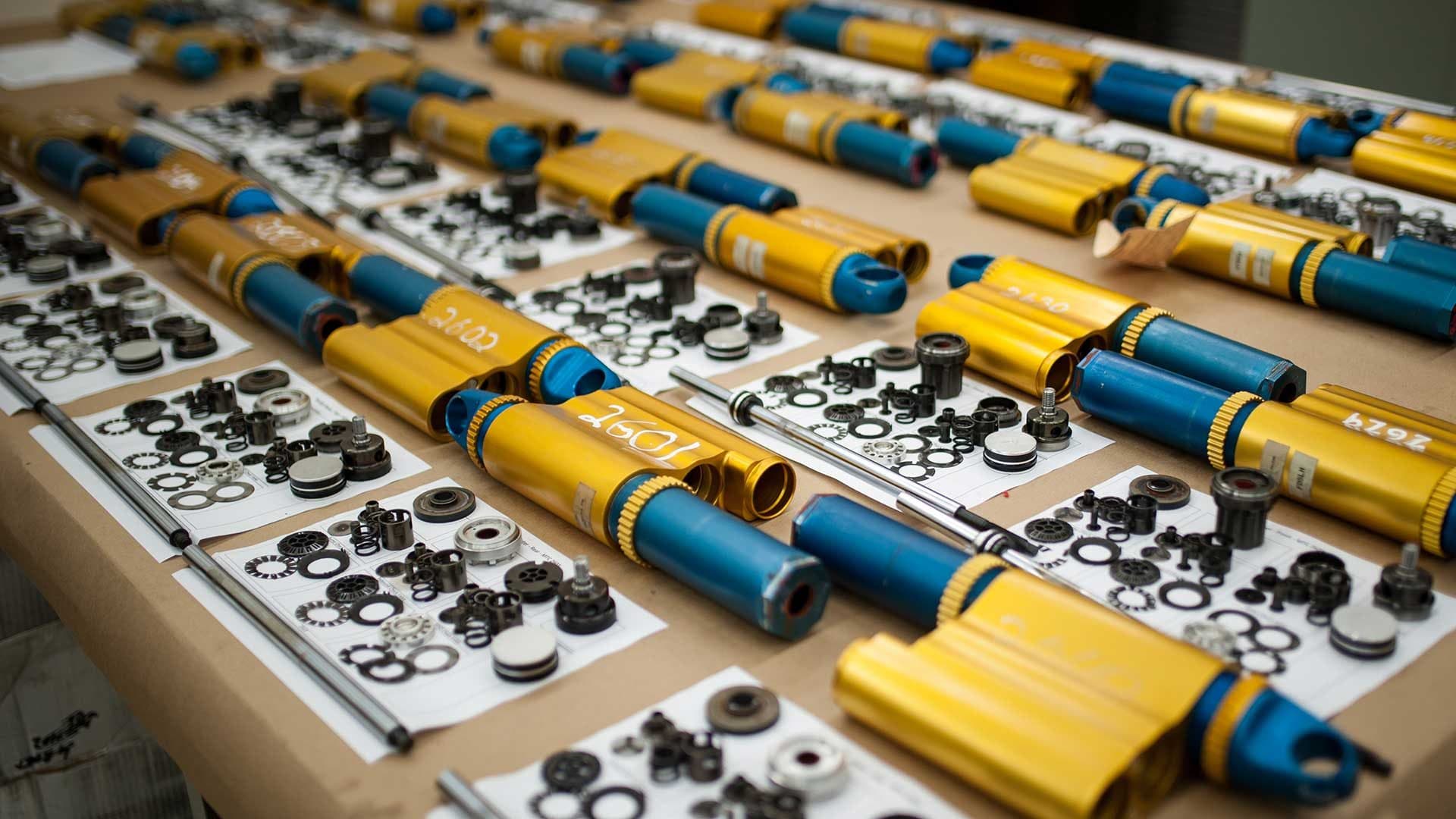
4. Validation: Component- and System-Level Testing
In-house fabrication and prototyping teams produced fully functional dampers. These were thoroughly tested on damper dynos (component-level validation) and on a multi-post rig (system-level validation).
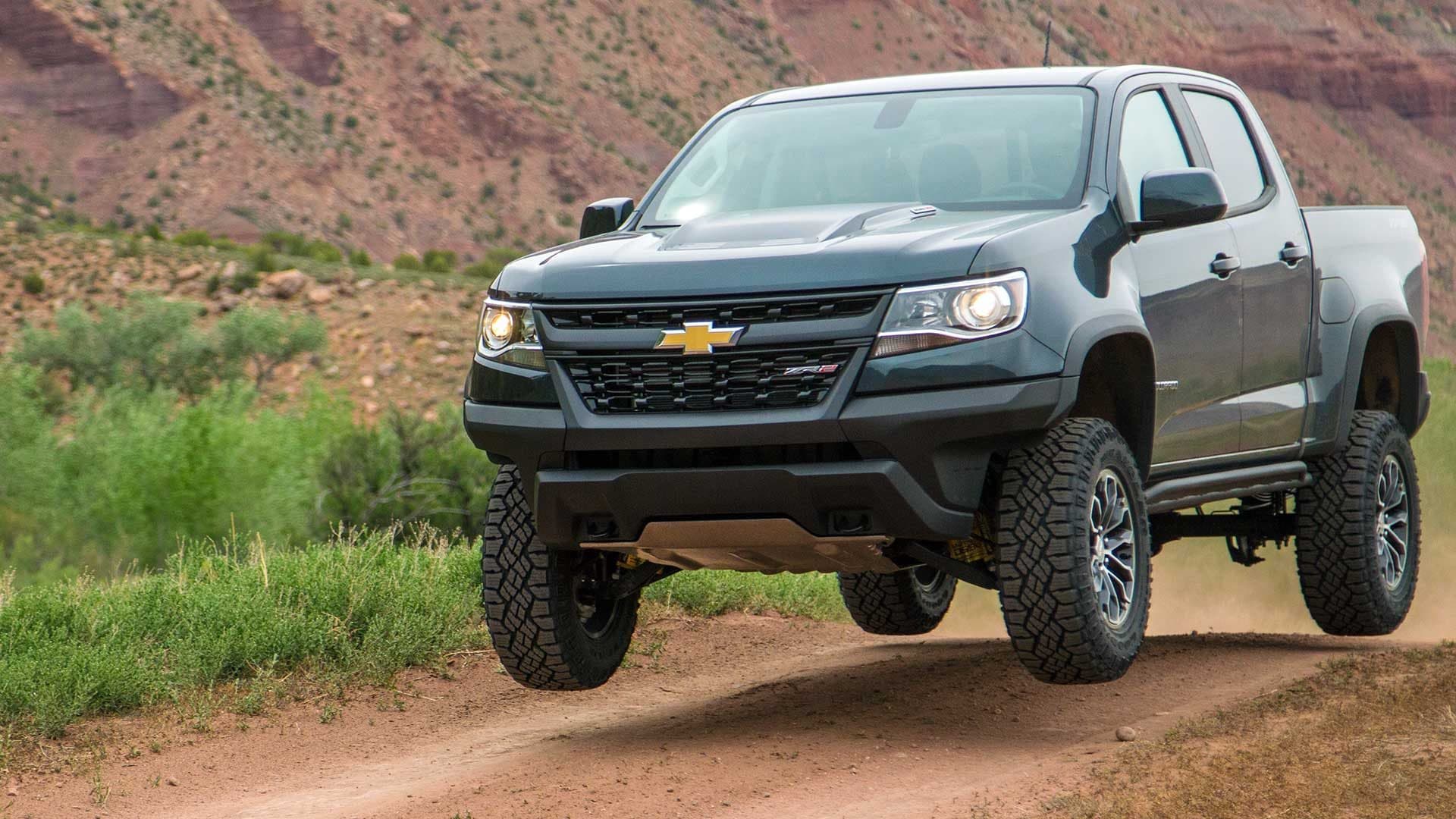
5. Validation: Vehicle-Level Testing
Dampers were installed on ZR2 prototypes and tested in real-world conditions including on-road driving, rock crawling and high-speed desert running. Performance was then compared against the original complete-vehicle specifications.
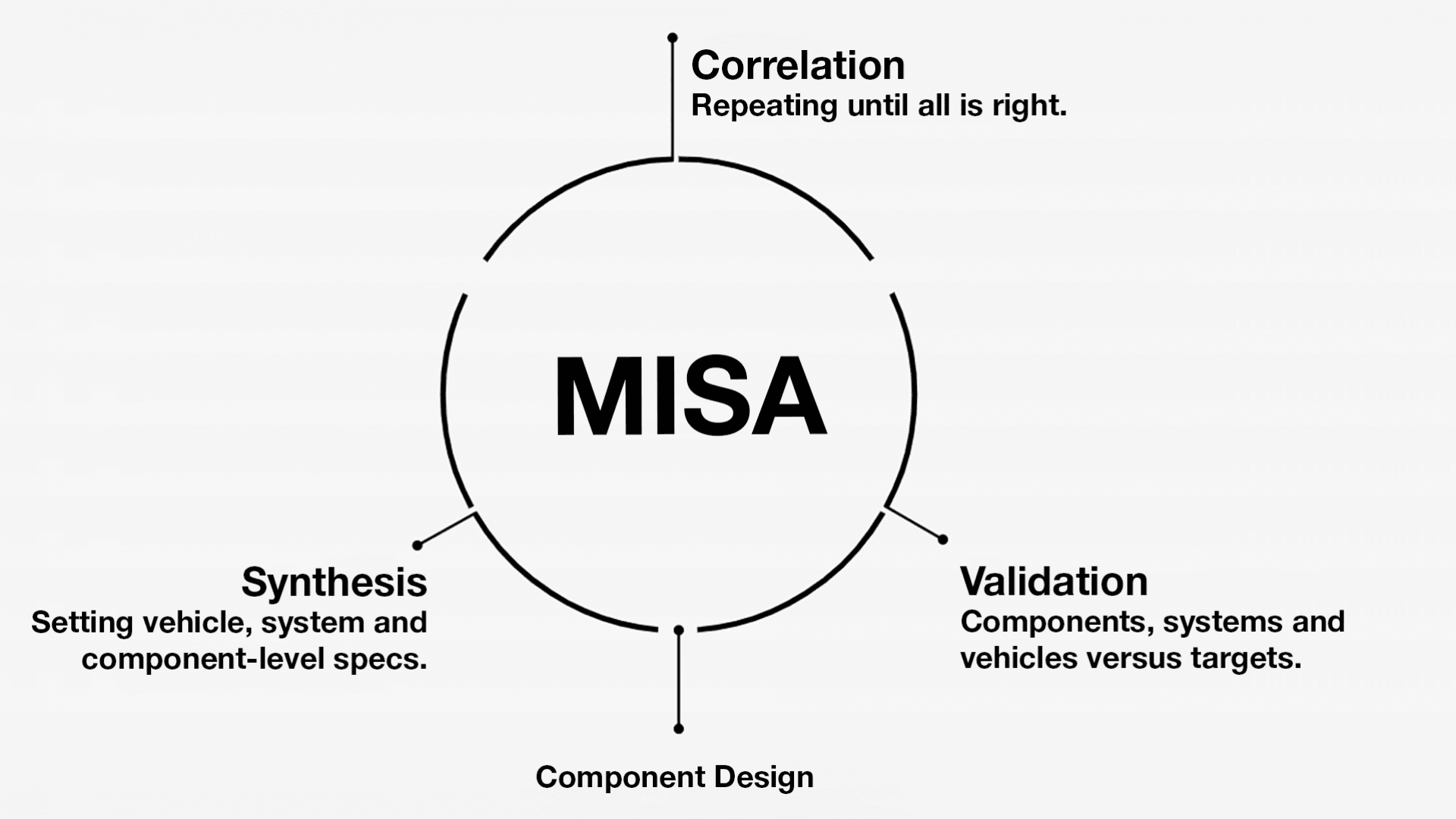
6. Correlation: Testing vs. Design Brief / Specification
Product and vehicle development is a repetitive process. MISA clearly defines targets and expectations, and then verifies achievements. The process identifies issues at all levels, to enable rapid problem solving.
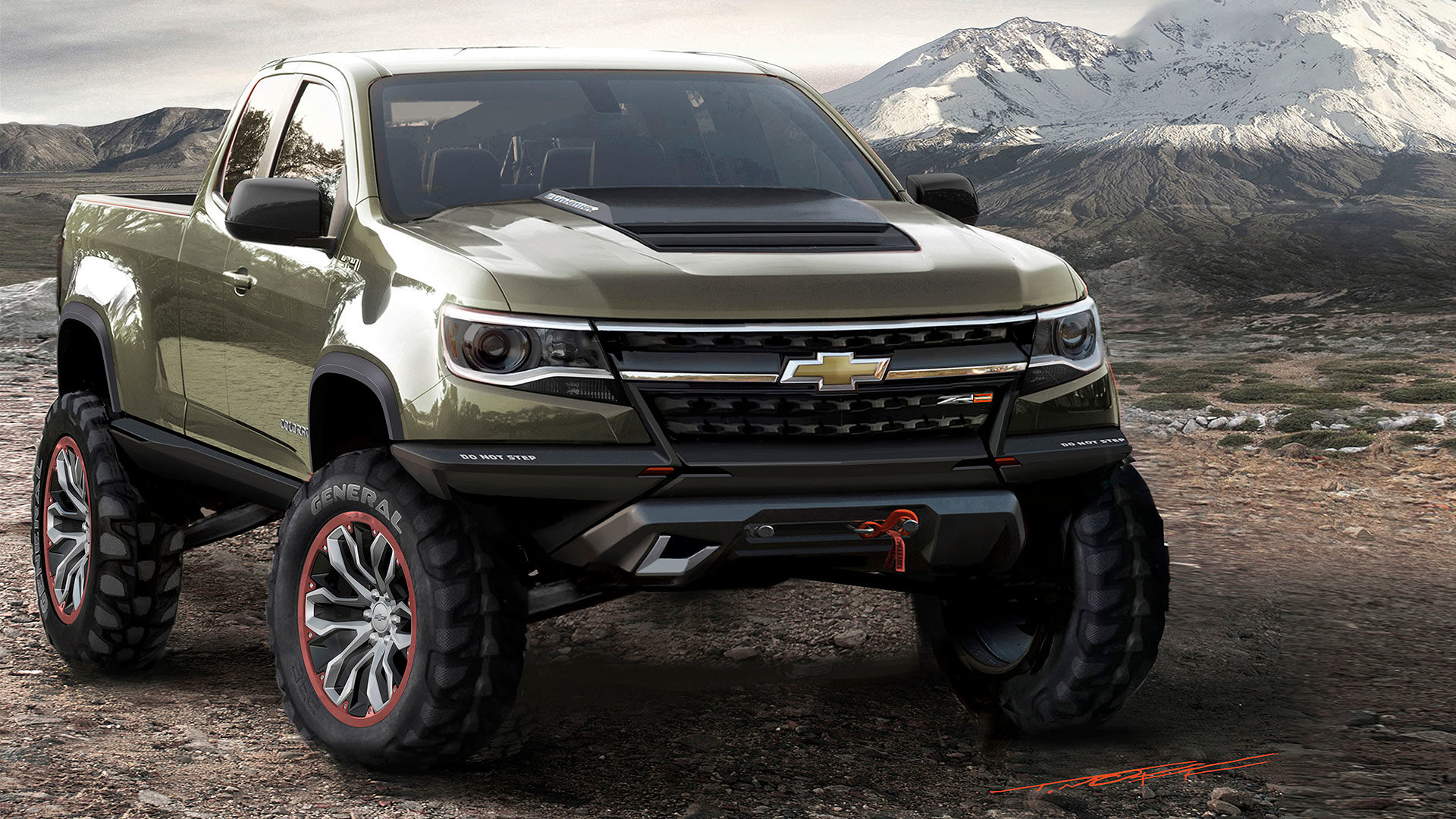
1. Synthesis: Design Brief and Vehicle-Level Specification
In collaboration with GM, the initial “Synthesis” phase defined a design brief and vehicle-level specification. This became the target against which vehicle performance was later measured.
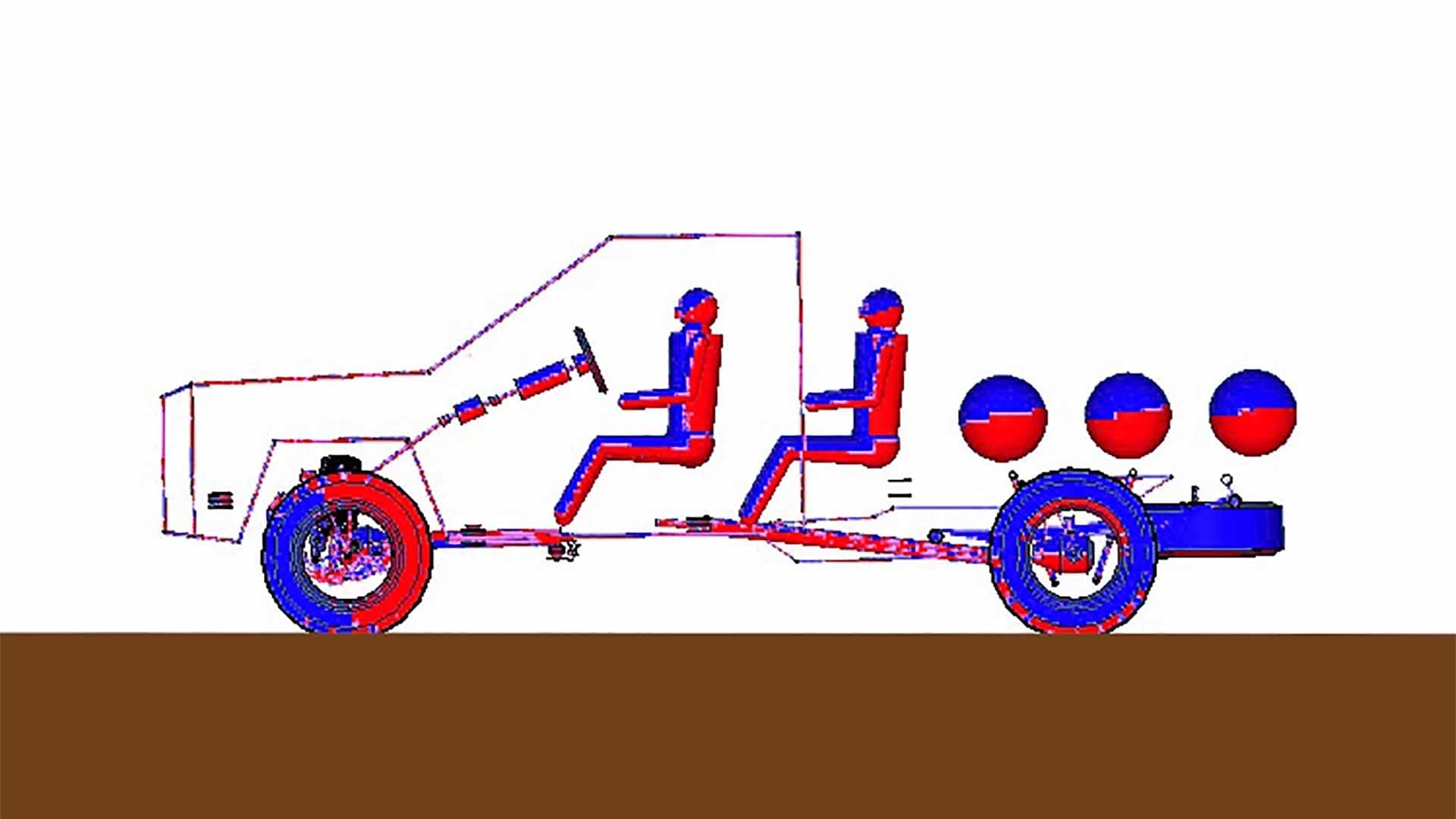
2. Synthesis: System- and Component-Level Specifications
In part two of the Synthesis phase, we analyzed all affected vehicle systems to develop system- and component-level specifications. System- and component-level performance were later measured against these targets.
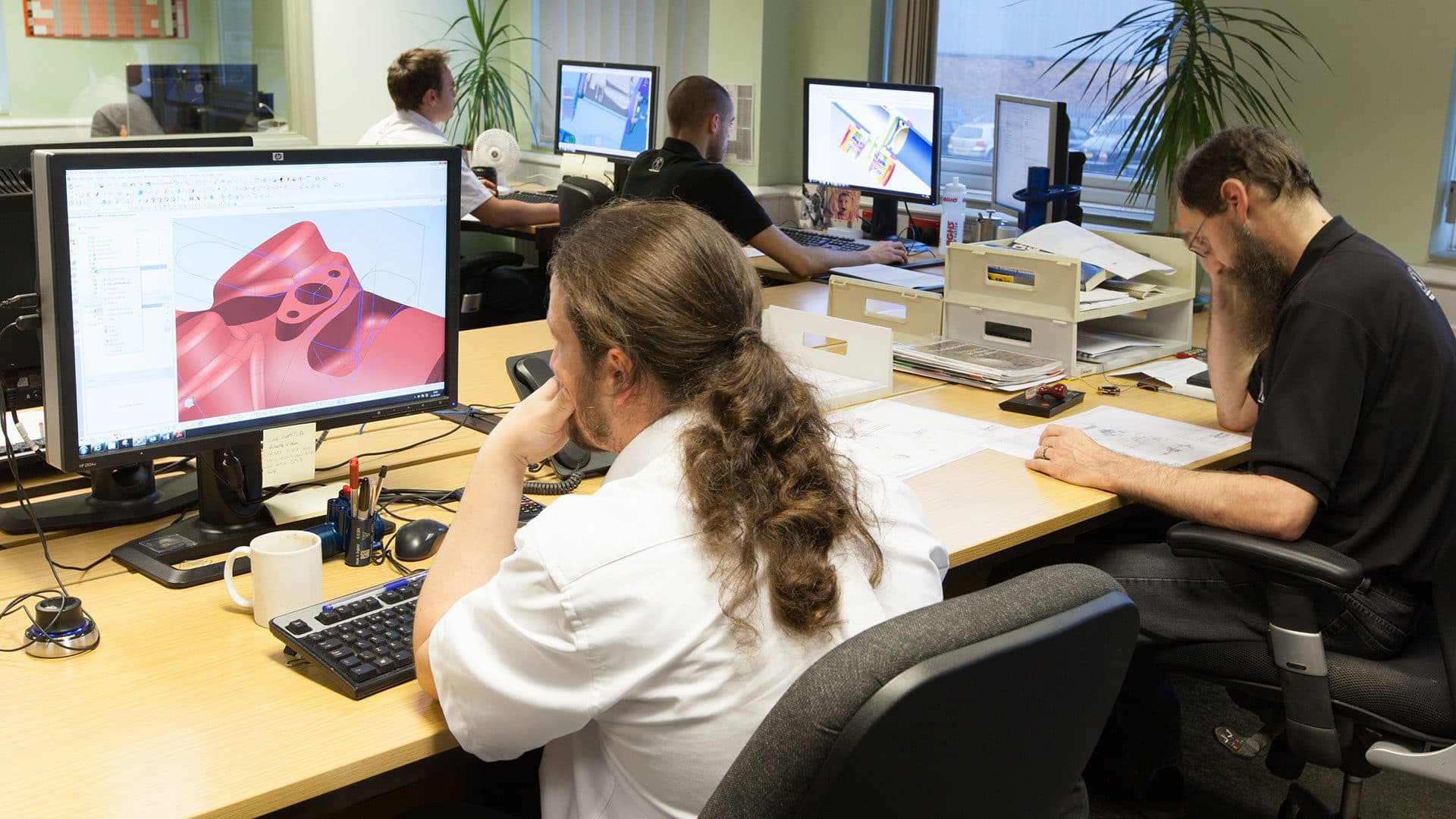
3. Component Design and Engineering
With specifications established, we moved into the design and engineering phase to develop a new Multimatic DSSV damper aimed at meeting the component-level specification.
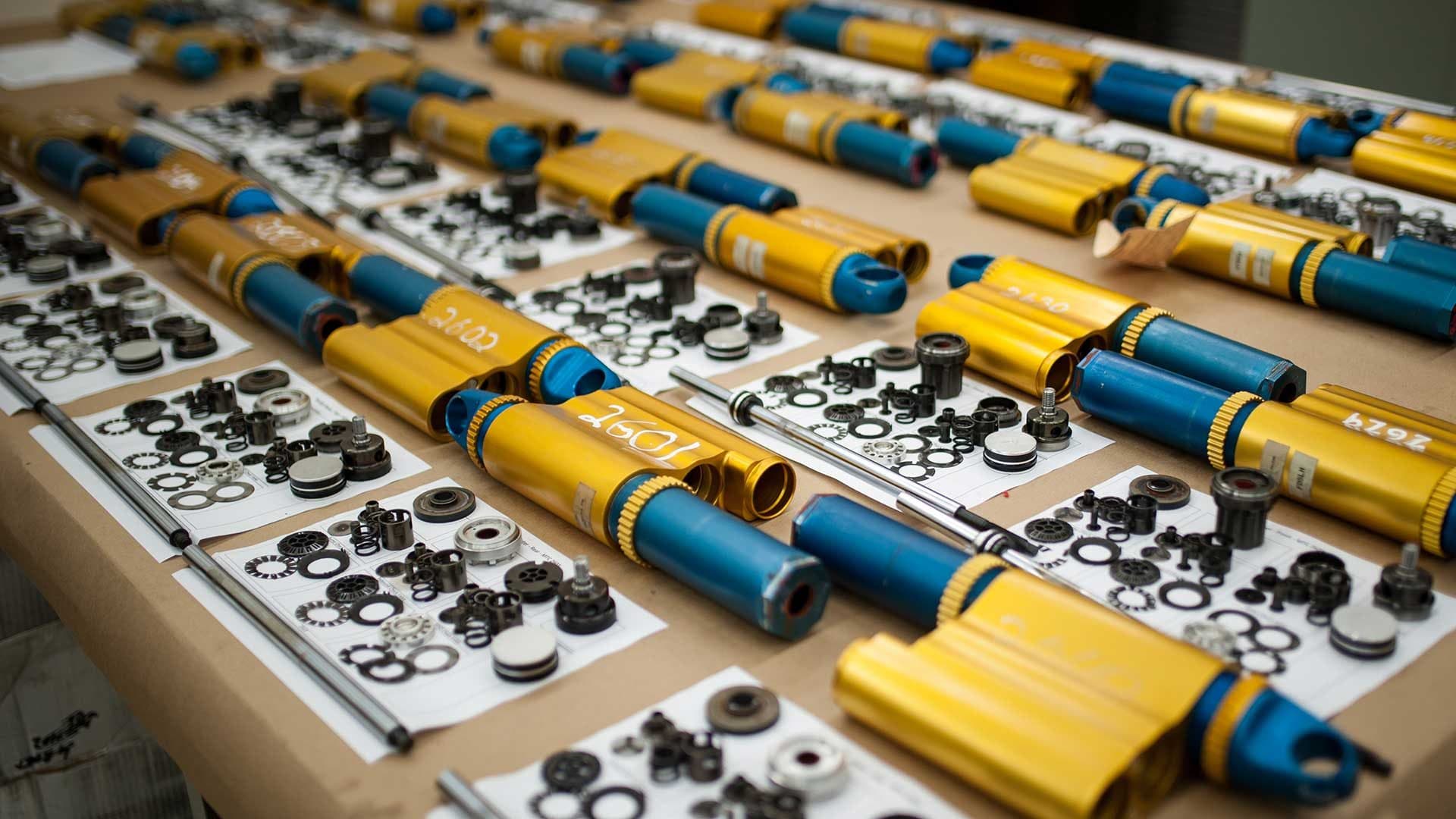
4. Validation: Component- and System-Level Testing
In-house fabrication and prototyping teams produced fully functional dampers. These were thoroughly tested on damper dynos (component-level validation) and on a multi-post rig (system-level validation).
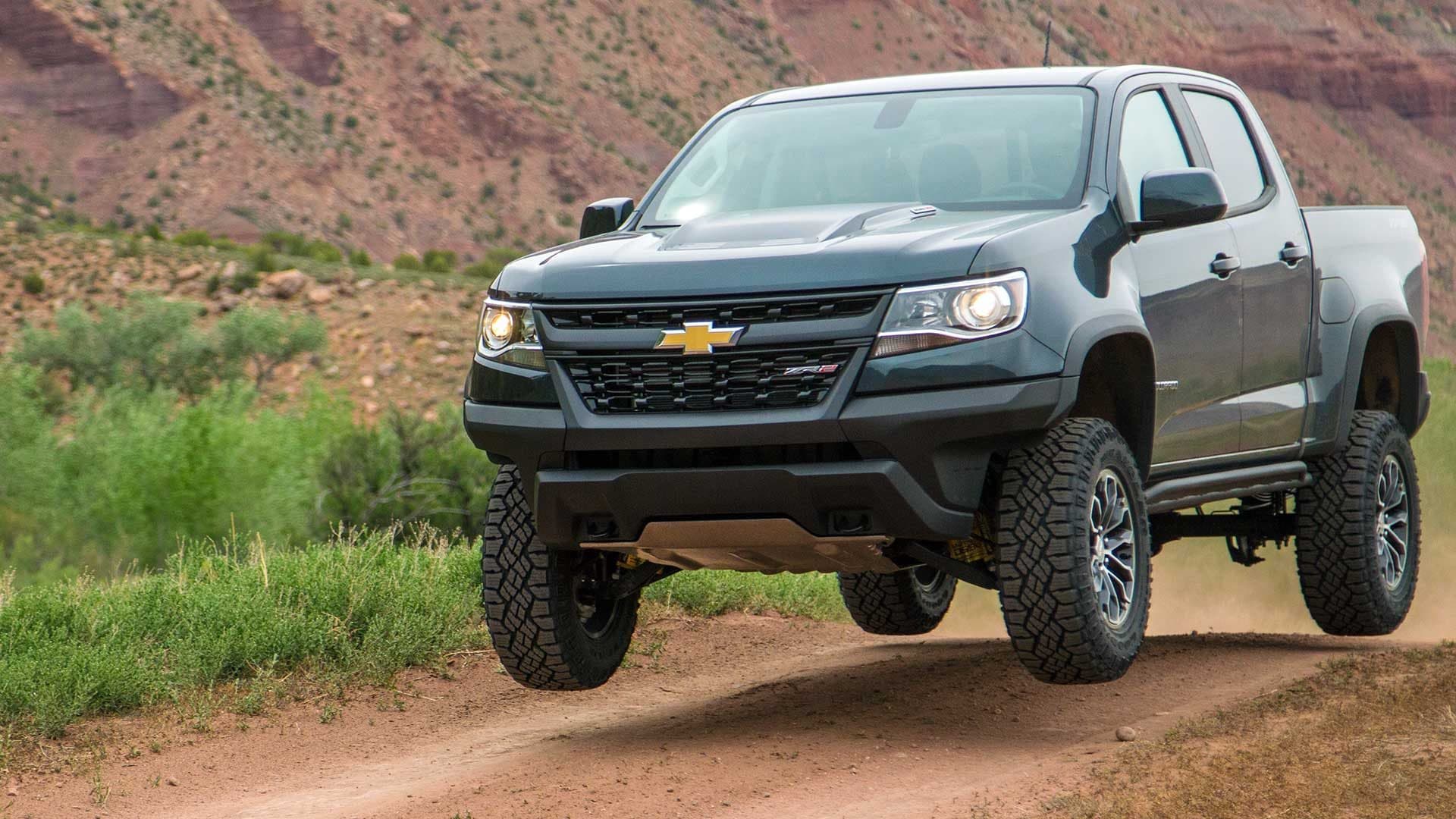
5. Validation: Vehicle-Level Testing
Dampers were installed on ZR2 prototypes and tested in real-world conditions including on-road driving, rock crawling and high-speed desert running. Performance was then compared against the original complete-vehicle specifications.
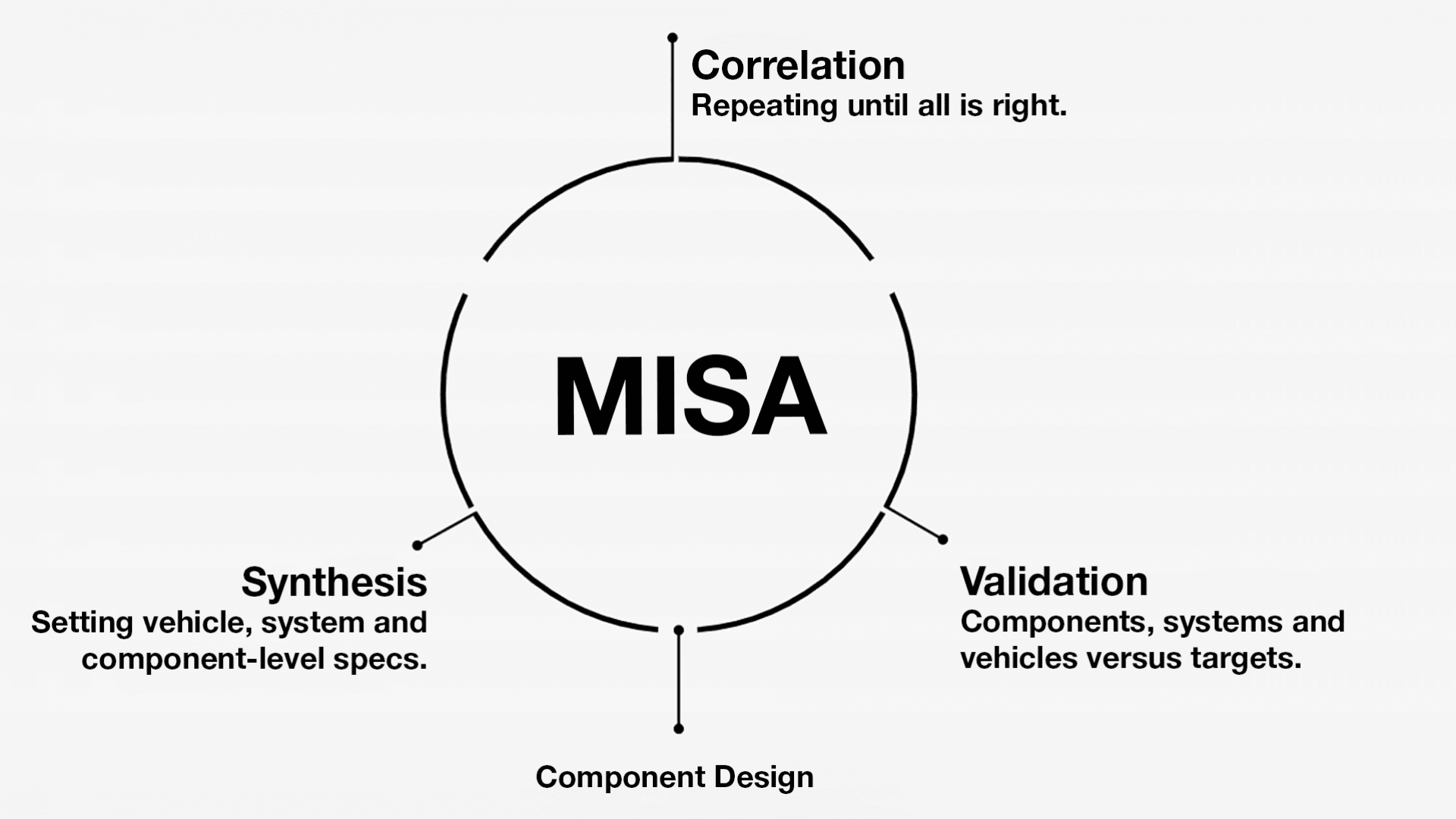
6. Correlation: Testing vs. Design Brief / Specification
Product and vehicle development is a repetitive process. MISA clearly defines targets and expectations, and then verifies achievements. The process identifies issues at all levels, to enable rapid problem solving.